Control of Volatile Organic Compounds from Automobile Refinishing Operations (250-RICR-120-05-30)
250-RICR-120-05-30 INACTIVE RULE
30.1 Purpose
The purpose of this regulation is to limit volatile organic compound emissions from automobile refinishing operations.
30.2 Authority
These regulations are authorized pursuant to R.I. Gen. Laws § 42-17.1-2(19) and Chapter 23-23, and have been promulgated pursuant to the procedures set forth in the R.I. Administrative Procedures Act, R.I. Gen. Laws Chapter 42-35.
30.3 Application
The terms and provisions of this regulation shall be liberally construed to permit the Department to effectuate the purposes of state laws, goals and policies.
30.4 Severability
If any provision of this regulation or the application thereof to any person or circumstance, is held invalid by a court of competent jurisdiction, the validity of the remainder of the regulation shall not be affected thereby.
30.5 Definitions
A. Unless otherwise expressly defined in this section, the terms used in this regulation shall be defined by reference to Part 0 of this Subchapter (General Definitions). As used in this regulation, the following terms shall, where the context permits, be construed as follows:
1. "Automobile refinishing" means any coating of Group I or Group II vehicles, their parts and components, or mobile equipment, including partial body collision repairs, for the purpose of protection or beautification and which is subsequent to the original coating applied at the plant coating assembly line.
2. "Anti-glare/Safety coating" means a low gloss coating formulated to eliminate glare for safety purposes on interior surfaces of a vehicle, as specified under the U.S. Department of Transportation Motor Vehicle Standards.
3. "Basecoat/clearcoat system" means a 2-stage topcoat system composed of a colored basecoat and a transparent final coat. For compliance purposes, the VOC content of basecoat/clearcoat systems is calculated according to the following formula:
VOC Tbc/cc= (VOCbc+2VOCcc)/3 |
Where: |
VOC Tbc/cc is the weighted average of the VOC content, in pounds VOC/gallon of coating, as applied, minus water, in the basecoat and clearcoat system. |
VOCbc is the VOC content, in pounds VOC/gallons of coating, as applied, minus water, of any given basecoat. |
VOCcc is the VOC content, in pounds VOC/gallons of coating, as applied, minus water, of any given clearcoat. |
4. "Catalyst" means a substance whose presence initiates the reaction between chemical compounds.
5. "Certified product data sheet" means documentation furnished by a coating supplier that provides the VOC content of an automobile refinishing coating in pounds of VOC per gallon of coating, as applied, minus water or of a surface preparation product, in pounds of VOC per gallon of material, as applied, including water, when mixed and used according to the manufacturer's recommendations. VOC content shall be measured using EPA Methods 24 and 311, or an equivalent or alternative method. The purpose of the Certified Product Data Sheet is to assist the facility in demonstrating compliance with the emission limitations presented in § 30.7 of this Part. Therefore, the VOC content should represent the maximum VOC emission potential of the automobile refinishing coating or surface preparation product. Charts provided by a manufacturer listing the VOC content, as applied, of several of the manufacturer's products will be considered acceptable Certified Product Data Sheets provided that they include the information specified in this definition.
6. "Coating applicator" means a device, mechanism, or apparatus used to apply a surface coating. Common types of application techniques include knife, roll, spray or dip.
7. "Coating line" means an operation or manufacturing process or device which may be comprised of one or more coating applicators, one or more flash-off areas and/or one or more ovens wherein a surface coating is dried and/or cured.
8. "Color match" means the ability of a repair coating to blend into an existing coating so that color difference is not visible.
9. "Electrostatic application" means the application of charged atomized paint droplets which are deposited by electrostatic attraction.
10. "Extreme performance coatings" means coatings intended for exposure to any of the following; outdoor weather conditions all of the time, temperatures frequently above 95ºC (203ºF), detergents, abrasive and scouring agents, solvents, corrosive atmospheres, or similar environmental conditions.
11. "Four stage coating system" means a topcoat system composed of a colored basecoat, two semi-transparent midcoats and a final transparent clearcoat. For compliance purposes, the VOC content of four stage coating systems is calculated according to the following formula:
VOC T4-stage= (VOCbc + VOCmc1 + VOCmc2 + 2VOCcc)/5 |
Where: |
VOC T4-stage is the weighted average of the VOC content, in pounds VOC/gallon of coating, as applied, minus water, in a basecoat, midcoat and clearcoat system. |
VOCbc is the VOC content, in pounds VOC/gallon of coating, as applied, minus water, of any given basecoat. |
VOCmc1 is the VOC content, in pounds VOC/gallon of coating, as applied, minus water, of the first midcoat. |
VOCmc2 is the VOC content, in pounds VOC/gallon of coating, as applied, minus water, of the second midcoat. |
VOCcc is the VOC content, in pounds VOC/gallon of coating, as applied, minus water, of any given clearcoat. |
12. "Group I vehicles" means passenger cars, large/heavy duty truck cabs and chassis, light and medium duty trucks and vans, and motorcycles.
13. "Group II vehicles and equipment" means public transit buses and mobile equipment.
14. "High volume low pressure spray" or "HVLP" means equipment used to apply coatings by means of a spray gun which operates at between 0.1 and 10 psig air pressure.
15. "Lacquer" means coating that dries primarily by solvent evaporation and is resoluble in its original solvent.
16. "Large/heavy duty trucks" means any truck having a manufacturer's gross vehicle weight rating of over 10,000 pounds.
17. "Light and medium trucks and vans" means any truck or van having a manufacturer's gross vehicle weight rating of 10,000 pounds or less.
18. "Mobile equipment" means any equipment which may be drawn or is capable of being driven on a roadway, including, but not limited to, truck bodies, truck trailers, utility bodies, camper shells, mobile cranes, bulldozers, street cleaners, golf carts and implements of husbandry.
19. "Oven" means a chamber within which heat is used to bake, cure or polymerize and/or dry a surface coating.
20. "Pretreatment" means any coating which contains a minimum of 0.5 percent acid by weight, is necessary to provide surface etching, and is applied directly to bare metal surfaces to provide corrosion resistance and adhesion.
21. "Primer" means any coating applied prior to the application of a topcoat for the purpose of corrosion resistance or adhesion.
22. "Primer sealer" means a coating that improves the adhesion of the topcoat, provides corrosion resistance, promotes color uniformity, and that resists penetration by the topcoat. "Primer sealer" includes a first coat applied to bare metal primarily for the purpose of preventing corrosion.
23. "Primer surfacer" means a coating that fills in surface imperfections and builds a film thickness in order to allow sanding.
24. "Reducer" means a solvent used to thin enamel.
25. "Specialty coating" means a product which is necessary due to unusual job performance requirements. These coatings or additives include, but are not limited to, adhesion promoters, uniform finish blenders, elastomeric materials, gloss flatteners, bright metal trim repair, and anti-glare coatings.
26. "Surface preparation product" means a product formulated to dissolve and remove tar, grease, wax, and other hydrophobic contaminants from a surface to be refinished.
27. "Three stage coating system" means a topcoat system composed of a colored basecoat, a semi-transparent midcoat and a final transparent clearcoat. For compliance purposes, the VOC content of three stage coating systems is calculated according to the following formula:
VOC T3-stage= (VOCbc + VOCmc + 2VOCcc)/4 |
Where: |
VOC T3-stage is the weighted average of the VOC content, in pounds VOC/gallon of coating, as applied, minus water, in a basecoat, midcoat and clearcoat system. |
VOCbc is the VOC content, in pounds VOC/gallon of coating, as applied, minus water, of any given basecoat. |
VOCmc is the VOC content, in pounds VOC/gallon of coating, as applied, minus water, of any given midcoat. |
VOCcc is the VOC content, in pounds VOC/gallon of coating, as applied, minus water, of any given clearcoat. |
28. "Topcoat" means the final film or series of films of coating applied to a surface and includes basecoat/clearcoat systems.
29. "Transfer efficiency" means the portion of coating solids which adhere to the substrate during the application process, expressed as a percentage of the total volume of coating solids delivered by the applicator.
30. "Utility body" means a special service compartment or unit that will be bolted, welded, or affixed onto an existing cab and chassis. The compartment may serve as storage for equipment or parts.
30.6 Applicability
A. The provisions of this regulation apply to any person who owns, leases, operates or controls an automobile refinishing facility. The provisions of § 30.7 of this Part shall also apply to any person who sells or offers for sale in Rhode Island any automobile refinishing coating or surface preparation product.
B. Wherever the term Volatile Organic Compound or VOC is used in §§ 30.6 through 30.12 and § 30.5 of this Part, this term should be read as Volatile Organic Compound and Halogenated Organic Compound or VOC and HOC.
30.7 Emission Limitations
A. Group I Vehicles
1. All coatings used for refinishing Group I vehicles, their parts and components, or Group II vehicles and mobile equipment where color match is required, must meet the emission limitations listed in Table 1:
TABLE 1 |
||
TYPE OF COATING |
EMISSION LIMITATION |
|
|
lb. VOC/gallon coating applied minus water |
lb. VOC/gallon solids applied |
Pretreatment |
6.5 |
55.6 |
Primer/Primer Surfacer |
4.8 |
13.8 |
Primer Sealer |
4.6 |
12.3 |
Topcoat |
5.0 |
15.6 |
Three or Four Stage Coating |
5.2 |
17.7 |
Specialty Coating |
7.0 |
143.1 |
2. For facilities complying without using add-on control equipment, the pounds of VOC per gallon of coating (minus water) limit must be met. For facilities which use add-on control equipment, the pounds of VOC/gallon of solids emission limit must be met.
B. Group II Vehicles
1. All used for refinishing Group II vehicles or their parts and components where color match is not required, must meet the emission limitations listed in Table 2:
TABLE 2 |
||
TYPE OF COATING |
EMISSION LIMITATION |
|
|
lb. VOC/gallon coating applied minus water |
lb. VOC/gallon of solids applied |
Pretreatment |
6.5 |
55.6 |
Primer/Primer Surfacer |
2.8 |
4.5 |
Primer Sealer |
3.5 |
6.7 |
Topcoat |
3.5 |
6.7 |
Extreme Performance Coating |
6.2 |
39.3 |
Specialty Coating |
7.0 |
143.1 |
2. For facilities complying without using add-on control equipment, the pounds of VOC per gallon of coating (minus water) limit must be met. For facilities which use add-on control equipment, the pounds of VOC/gallon of solids emission limit must be met.
C. Compliance with the emission limitations of §§ 30.7(A) and 30.7(A)(1) of this Part shall be achieved through:
1. Use of coatings which comply with the applicable emission limitations listed in §§ 30.7(A) and 30.7(A)(1) of this Part for all coatings used, or,
2. Installation of a control system which has been approved by the Department and which reduces the total VOC emissions from the facility by 95 percent or greater as compared to uncontrolled VOC emissions, or,
3. Installation of a control system which has been approved by the Department and which reduces VOC emissions to the equivalent of the emission limitations of §§ 30.7(A) and 30.7(A)(1) of this Part as calculated on a solids applied basis, or,
4. An alternative equivalent method of control as approved by the Director. Any alternative method approved by the Director must also be approved by EPA as a source specific State Implementation Plan (SIP) revision.
D. All surface preparation products, except for surface preparation products which are used exclusively on plastic surfaces, shall have a VOC content which does not exceed 1.4 pounds VOC/gallon of material as applied including water. Surface preparation products which are used exclusively on plastic surfaces shall have a VOC content which does not exceed 6.5 pounds VOC/gallon of material as applied including water.
E. No person shall sell or offer for sale in Rhode Island any automobile refinishing coating or surface preparation product that does not comply with the applicable emission limitations in §§ 30.7(A), 30.7(A)(1) and 30.7(B) of this Part. This provision does not apply to the following:
1. Sale of automobile refinishing coatings and surface preparation products supplied in containers having capacities less than one pint,
2. Sale of automobile refinishing coatings or surface preparation products for use in applications other than automobile refinishing,
3. Sale of automobile refinishing coatings or surface preparation products for use outside of the State of Rhode Island,
4. Sale of automobile refinishing coatings to facilities which are equipped with and are operating a control system provided that:
a. The control system is in compliance with the specifications in § 30.7(A)(2) of this Part, and,
b. The buyer provides the seller with a copy of the Department’s approval of the control system, and,
c. The seller maintains the copy of the approval for a period of three (3) years and makes it available for inspection by the Department or the EPA, upon request.
F. Any person selling an automobile refinishing coating or surface preparation product in Rhode Island shall provide the buyer with a copy of a Certified Product Data Sheet for that material, as defined in § 30.5 of this Part.
30.8 Equipment Specifications
A. No person shall engage in automobile refinishing unless one of the following methods is used:
1. Electrostatic application equipment, operated in accordance with the manufacturer's recommendations; or,
2. High Volume Low Pressure (HVLP) spray equipment, operated in accordance with the manufacturer's recommendations; or,
3. Another type of application which achieves a transfer efficiency of at least 65% and has been approved by the Director.
B. All spray guns must be cleaned in a device that meets the following specifications:
1. Solvent must be recirculated during the cleaning process so that the solvent is used until it no longer cleans guns satisfactorily; and,
2. Spent solvent must be collected so it is available for disposal; and,
3. The device must be vapor tight during cleaning, rinsing and draining operations or must achieve equivalent emissions reductions and be approved by the Director.
C. Fresh and spent solvent, cloth or paper which has been used for solvent surface preparation and cleanup, waste paint, and sludge must be stored in closed containers. Disposal of such materials must be in accordance with applicable hazardous waste and solid waste regulations.
30.9 Recordkeeping and Reporting
A. On and after the compliance dates specified in § 30.12(A) of this Part, the owner or operator of an automobile refinishing facility shall collect and record all of the following information and maintain the information at the facility for a period of three (3) years. These records shall be made available to the Department and EPA upon request.
1. The name, identification number and manufacturer of each coating, reducer, catalyst surface preparation product, and cleanup solvent used at the facility;
2. The volume of each coating, reducer, surface preparation product, and cleanup solvent used at the facility each month;
3. Certified Product Data Sheets showing the VOC content, in pounds of VOC/gallon of coating, excluding water, as applied, of each coating used at the facility;
4. Certified Product Data Sheets showing the VOC content, in pounds of VOC/gallon of material, including water, as applied, of each surface preparation product used at the facility;
5. For each basecoat/clearcoat, three stage coating, and four stage coating system used, the weighted average VOC content of the coating, calculated as specified in § 30.5 of this Part;
6. A daily log of operating time for any capture system, control device, monitoring equipment, and the associated coating line or operation;
7. A maintenance log for any capture system, control device, and monitoring equipment detailing all routine and non-routine maintenance performed including dates and duration of any outages;
8. For thermal incinerators:
a. All 3‑hour periods of operation in which the average combustion temperature was more than 28ºC (50ºF) below the average combustion temperature during the most recent performance test that demonstrated that the facility was in compliance, and,
b. The operating temperature.
9. For catalytic incinerators:
a. All periods where the temperature increase across the catalyst bed is less than 80% of the temperature increase recorded during the most recent performance test that demonstrated that the facility was in compliance, and,
b. The inlet and outlet temperatures and temperature rise across the catalyst bed.
10. For carbon adsorbers:
a. All 3-hour periods of operation during which the average VOC concentration or reading of organics in the exhaust gases is more than 20 percent greater than the average exhaust gas concentration or reading measured by the organics monitoring device during the most recent determination of the recovery efficiency of the carbon adsorber that demonstrated that the facility was in compliance, and,
b. The pressure drop across the adsorber and the hydrocarbon levels for breakthrough.
30.10 Registration
A. All facilities which perform automobile refinishing must register annually with the Office of Air Resources. No later than 45 days following the end of a calendar year, the following information must be submitted on forms supplied by the Department:
1. The name and address of the facility and the name and telephone number of a responsible corporate official submitting the registration, and,
2. A description of all operations in the facility from which volatile organic compounds are emitted, and,
3. Quantities of coatings, solvents, dissolvers, viscosity reducers, diluents, thinners, reagents, cleaning agents, enamels, lacquers, or paints consumed during the calendar year of record, and,
4. The amount of volatile organic compound per gallon of coating solution (pounds per gallon) for each coating, enamel, lacquer, or paint consumed at the facility during the calendar year of record.
30.11 Compliance Demonstration/Testing
A. Compliance with emission limitations of §§ 30.7(A), 30.7(A)(1), and 30.7(B) of this Part shall be demonstrated upon request of the Director in accordance with 40 C.F.R. § 60, Appendix A, Methods 24, 24A, 25 or any other EPA approved method which has been accepted by the Director. A one hour bake time must be used for Methods 24 and 24A. Methods 24 and 24A apply to multicomponent coatings.
B. (Reserved for stack exhaust sampling techniques.)
C. Facilities using control equipment to comply with the emission limitations of §§ 30.7(A) and 30.7(A)(1) of this Part must show that the equipment meets specific capture and control efficiency limits which will be set in an enforceable document. Compliance must be demonstrated upon equipment start up and thereafter upon request of the Director. Control efficiency of the equipment shall be determined using EPA-approved test methods. Calculations shall be done on a solids applied basis. Compliance averaging times shall be met according to the control device chosen and EPA test methods (as codified in 40 C.F.R. § 60), as follows:
TABLE 3 |
||
Compliance Method |
EPA Reference Test Method |
Test Averaging Time |
Solvent destruction or solvent recovery except carbon adsorption |
25 |
3 hours |
Carbon adsorption |
25 or other test method as appropriate |
The length of adsorption cycle or 24-hours, which-ever is less. |
1. or other methods approved by the Department and EPA. Once the control efficiency has been determined for any control device by Reference Method 25, or any alternative method approved by the Department and EPA, compliance shall be determined on an instantaneous basis time period (e.g. determined control efficiency shall be used to calculate whether samples from the process meet the applicable emissions limit.) Continuous compliance will be maintained at all times.
D. Compliance with transfer efficiency requirements specified in § 30.8(A)(3) of this Part shall be demonstrated using a method acceptable to the Department and EPA.
30.12 Compliance Schedule
A. Persons owning, leasing or controlling the operation of any automobile refinishing facility shall achieve compliance with the requirements of this regulation no later than July 1, 1995. All automobile refinishing operations commencing operation after July 1, 1994 must be in compliance with the emission limits specified in §§ 30.7(A) and 30.7(A)(1) of this Part upon commencing operation.
B. Within fifteen (15) days of achieving compliance with §§ 30.7 and 30.8 of this Part, the owner or operator of the facility shall certify to the Director in writing that compliance has been achieved. Such certification shall be signed by the owner or operator of the facility, and shall include the date that compliance was achieved.
Title | 250 | Rhode Island Department of Environmental Management |
Chapter | 120 | Air Resources |
Subchapter | 05 | Air Pollution Control |
Part | 30 | Control of Volatile Organic Compounds from Automobile Refinishing Operations (250-RICR-120-05-30) |
Type of Filing | Technical Revision |
Regulation Status | Inactive |
Effective | 07/19/2007 to 01/04/2022 |
Regulation Authority:
R.I. Gen. Laws § 42-17.1-2(19) and Chapter 23-23
Purpose and Reason:
This Technical Revision is being promulgated to correct formatting issues. The indentation and citation formats were corrected throughout the document and the paragraph levels were re-labeled in Sections 30.5, 30.7, 30.9, 30.10, and 30.11. No substantive changes were made.
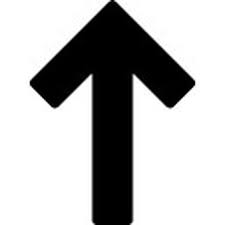
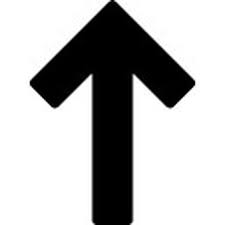
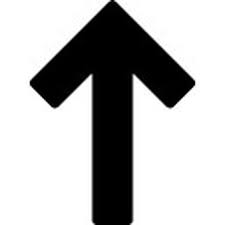
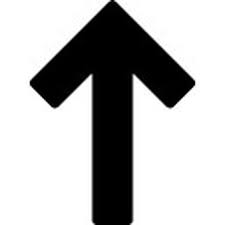
Rulemaking Documents are organized by document type and are part of this rule’s rulemaking record (R.I. Gen. Laws § 42-35-2.3). If multiple documents of the same type are listed below, each is a unique document. If there are multiple Public Notice of Proposed Rulemaking documents, view each document to identify the most recently amended version, as it may be amended at any point during the Public Comment Period.