Air Pollution Control Regulation No. 23 - Control of Perchloroethylene Emissions from Dry Cleaning Operations
250-RICR-120-05-23 INACTIVE RULE
23.1 Purpose and Authority
23.1.1 Purpose
The purpose of this regulation is to limit perchloroethylene emissions from dry cleaning operations.
23.1.2 Authority
These regulations are authorized pursuant to R.I. Gen. Laws § 42-17.1-2(19) and R.I. Gen. Laws Chapter 23-23, and have been promulgated pursuant to the procedures set forth in the Rhode Island Administrative Procedures Act, R.I. Gen. Laws Chapter 42-35.
23.2 Application
The terms and provisions of this regulation shall be liberally construed to permit the Department to effectuate the purposes of state laws, goals and policies.
23.3 Severability
If any provision of this regulation or the application thereof to any person or circumstance, is held invalid by a court of competent jurisdiction, the validity of the remainder of the regulation shall not be affected thereby.
23.4 Definitions
A. Unless otherwise expressly defined in this section, the terms used in this regulation shall be defined by reference to Part 0 of this Subchapter (General Definitions). As used in this regulation, the following terms shall, where the context permits, be construed as follows:
1. “Articles” means clothing, garments, textiles, fabrics, leather goods, and similar materials.
2. “Carbon adsorber” means a dry cleaning control system that consists of an inlet for exhaust gases; activated carbon in the form of a fixed bed, cartridge or canister as an adsorbent and an outlet for exhaust gases; and a system to strip or desorb solvent from the saturated adsorbent.
3. “Closed-loop machine” means a dry-to-dry machine that recirculates perchloroethylene-laden vapor through a refrigerated condenser and that does not exhaust to the atmosphere during the drying cycle. A closed-loop machine may allow venting to the ambient air through a local exhaust ventilation system, such as a door fan, after the drying cycle is complete and the machine door is open.
4. “Co-located” means sharing a common wall, floor, or ceiling with a residence or a separately owned business.
5. “Colorimetric detector tube” means a glass tube which is designed to measure the concentration of perchloroethylene in air drawn through the tube and that contains a sorbent material which is impregnated with a chemical that is sensitive to perchloroethylene.
6. “Cool-down” means the portion of the drying cycle that begins when the heating mechanism deactivates. During the cool-down period, the refrigerated condenser continues to reduce the temperature of the air circulating through the drum to reduce the concentration of perchloroethylene in the drum.
7. “Day care center” means any person, firm, corporation, association or agency who, on a regular or irregular basis, receives any child under the age of sixteen (16) years, for the purpose of care and/or supervision, apart from their parent or guardian, for any part of a 24-hour day.
8. “Desorption” means the regeneration or stripping of a carbon adsorber of the adsorbed solvent using hot air, steam or other means.
9. “Distillation unit” means a device used to volatilize and recover perchloroethylene from contaminated perchloroethylene.
10. “Diverter valve” means a flow control device that prevents room air from passing through a refrigerated condenser when the door of a dry cleaning machine is open.
11. “Door fan” means a local exhaust ventilation system that pulls room air into the dry cleaning machine when the machine door is open.
12. “Drum” means the rotating cylinder or wheel of the dry cleaning machine that holds the articles being cleaned.
13. “Dry cleaning” means a process used to remove soil, grease, paint and other unwanted substances from articles using perchloroethylene as a solvent.
14. “Dry cleaning control system” means equipment used to reduce the amount of perchloroethylene in an air stream prior to discharge to the atmosphere.
15. “Dry cleaning system” means all equipment, devices or apparatus associated with dry cleaning operations including, but not limited to: dry-to-dry machines; transfer machine systems; perchloroethylene filter and purification systems; perchloroethylene waste holding, treatment and disposal systems; perchloroethylene supply systems; dip tanks; pumps; gaskets, piping, ducting, fittings, valves or flanges that convey liquid perchloroethylene or perchloroethylene-contaminated air; and dry cleaning control systems.
16. “Dry-to-dry machine” means a dry cleaning operation in which washing and drying are performed in the same machine.
17. “Dryer” means a machine used to remove perchloroethylene from articles by tumbling them in a heated air stream.
18. “Drying cycle” means the portion of a dry cleaning machine’s operating cycle in which the perchloroethylene remaining in the articles after washing and extraction is actively removed. The drying cycle begins when the heating coils are activated and ends when the machine ceases rotation of the drum.
19. “Drying sensor” means a device that senses the perchloroethylene concentration in the drying air or the liquid solvent recovery rate. The drying sensor automatically extends the drying cycle for a set time beyond the activation point to ensure that the articles are dry before being removed from the machine. Drying sensors include, but are not limited to: infrared analyzers, float switches, and resistance probes.
20. “Exhaust damper” means a flow control device that prevents the air-perchloroethylene gas-vapor stream from exiting the dry cleaning machine and flowing into a carbon adsorber before room air is drawn into the dry cleaning machine.
21. “Filter” means a porous device through which perchloroethylene is passed to remove contaminants in suspension. Examples of filters include, but are not limited to, lint filter (button trap), cartridge filter, tubular filter, regenerative filter, prefilter, polishing filter, and spin disc filter.
22. “Heating coil” means the device used to heat the air stream circulated from the dry cleaning machine drum after perchloroethylene has been condensed from the air stream and before the stream reenters the dry cleaning machine drum.
23. “Muck cooker” means a device for heating material trapped by a filter in a dry cleaning machine for the purpose of driving off perchloroethylene vapors for reclaiming.
24. "Perchloroethylene dry cleaning facility" means a facility engaged in dry cleaning using perchloroethylene. The facility includes, but is not limited to, any dry cleaning system and attendant stacks.
25. “Primary carbon adsorber” means a carbon adsorber used to control process vent emissions from a transfer machine system or a dry-to-dry machine that is not a closed-loop machine.
26. “Reclaimer” means a machine used to remove perchloroethylene from articles by tumbling them in a heated air stream.
27. “Refrigerated condenser” means a dry cleaning control system that removes condensable vapors from a gas-vapor stream by cooling the vapors using a mechanical refrigerated system.
28. “Secondary carbon adsorber” means a carbon adsorber that is designed to further reduce the perchloroethylene concentration in the gas-vapor stream after the stream is cooled by a refrigerated condenser.
29. “Transfer machine system” means a multiple-machine dry cleaning operation in which washing and drying are performed in different machines. Examples include, but are not limited to:
a. A washer and dryer(s);
b. A washer and reclaimer(s); or
c. A dry-to-dry machine and reclaimer(s).
30. “Water separator” means a vessel that uses gravity to physically separate liquid perchloroethylene from liquid water.
23.5 Applicability
The provisions of this regulation apply to all perchloroethylene dry cleaning facilities.
23.6 Compliance Certification
A. Prior to installation of perchloroethylene dry cleaning equipment, the owner of a dry cleaning facility must certify to the Director, in writing and on a form provided by the Department, that the proposed installation complies with the requirements of this regulation. The certification must be signed by the owner of the facility.
B. If the ownership of a perchloroethylene dry cleaning facility changes, the new owner must notify the Department in writing within forty-five (45) days that the change has occurred. The notification shall include the name and address of the facility, the name of the new owner or operator, and a certification, signed by the new owner, that the facility is in compliance with the requirements of this regulation.
C. The owner of any facility that modifies a dry cleaning system or any part of a dry cleaning system shall certify in writing to the Department before beginning operation of the modified equipment that the modified dry cleaning system is in compliance with this regulation.
D. All dry cleaning machines must be in compliance with the requirements of this regulation upon start-up.
23.7 Equipment Requirements
A. All perchloroethylene dry cleaning machines shall be closed-loop dry-to-dry machines equipped with a refrigerated condenser and either:
1. A secondary carbon adsorber and drying sensor, such that the perchloroethylene vapor-gas stream passes through the carbon adsorber immediately before the door of the dry cleaning machine is opened; or
2. A door fan/local exhaust ventilation system.
B. No person shall operate a transfer dry cleaning system or a dry-to-dry machine that is not a closed-loop machine after December 2, 2005. All transfer machines and dry-to-dry machines that are not closed-loop machines must be removed from the facility or made permanently inoperable by that date.
23.8 Specifications for Refrigerated Condensers and Drying Sensors
A. Refrigerated condenser and drying sensors operated to comply with § 23.7 of this Part shall adhere to the following specifications:
1. The outlet temperature of the air-vapor stream downstream of any by-pass of the refrigerated condenser shall not exceed forty-five degrees Fahrenheit (45°F) during the final cool-down cycle. The door of the dry cleaning machine shall not be opened until the temperature of the stream is at or below forty-five degrees Fahrenheit (45°F), as indicated by a temperature gauge meeting the specifications of § 23.8(A)(2) of this Part;
2. A dry cleaning system with a refrigerated condenser must be equipped with a temperature gauge that measures the temperature of the outlet vapor stream downstream of any by-pass of the condenser and that is easily visible to the operator. The temperature gauge must be designed to measure a temperature of forty-five degrees Fahrenheit (45°F) with an accuracy of ± two degrees Fahrenheit (2°F);
3. Dry cleaning equipment equipped with a refrigerated condenser shall not vent or release the gas-vapor stream while the drum is rotating;
4. Refrigerated condensers shall be certified by the manufacturer to reduce the perchloroethylene concentration in the drum to no more than eight thousand six hundred (8600) ppm upon completion of the drying cycle.
5. Drying sensors shall extend the drying time in the drying cycle at least four (4) minutes beyond the time that the solvent recovery rate is less than forty (40) ml/min or the solvent concentration in the drum is less than eight thousand six hundred (8600) ppm perchloroethylene;
6. Refrigerated condensers on machines equipped with a door fan/local exhaust must be operated with a diverter valve which prevents room air from passing through the condenser when the door of the dry cleaning machine is open; and
7. The machine operator shall record the temperature of the air-vapor stream as measured by the temperature gauge at least one time each calendar week.
23.9 Specifications for Door Fan/Local Exhaust Systems
A. Door fan/local exhaust systems operated pursuant to § 23.7(A)(2) of this Part shall adhere to the following requirements:
1. The door fan/local exhaust system must include a mechanical exhaust fan that is activated when the loading door is open, drawing air from the machine drum to an exhaust and causing room air to be drawn in through the loading door;
2. A minimum inward air velocity of one hundred (100) fpm must be maintained through the door opening area of the loading door of the machine. The velocity much be checked at least once per week using a portable velometer or an equivalent device;
3. The door fan/local ventilation system must not recirculate vapors and must be vented to the outdoor air;
4. The door fan/local exhaust ventilation emissions must be controlled to a design emission standard of five (5) ppm perchloroethylene and an in-use maximum compliance standard of twenty (20) ppm;
5. The owner or operator shall provide a sampling port in the exhaust ductwork which is:
a. Easily accessible;
b. Downstream of any emissions control device;
c. Upstream of any other inlet to the ductwork; and
d. To the maximum extent possible, at least eight (8) stack or duct diameters downstream and at least two (2) stack or duct diameters upstream of any flow disturbance such as a bend, expansion, contraction, or outlet in the ductwork, unless this is not possible given the physical layout of the facility. If it is not possible to locate the sampling port eight (8) stack or duct diameters downstream and two (2) stack or duct diameters upstream of any flow disturbance, the port should be located at a point as near to those parameters as possible.
B. The owner or operator of the facility shall measure the perchloroethylene concentration in the exhaust stream weekly at the sampling port specified in § 23.9(A)(5) of this Part, using the following procedures:
1. A colorimetric detector tube capable of measuring a concentration of twenty (20) ppm to an accuracy of ± five (5) ppm shall be used;
2. Colorimetric detector tubes shall be used according to the manufacturer’s instructions; and
3. If a carbon adsorber is used to reduce the perchloroethylene concentration in the exhaust stream, the measurement shall be performed just prior to a planned desorption of the carbon adsorber.
23.10 Requirements for Carbon Adsorbers
A. A secondary carbon adsorber operated to comply with § 23.7(A)(1) of this Part shall adhere to the following requirements:
1. The carbon adsorber must be designed to function with a refrigerated condenser complying with the specifications in § 23.8 of this Part;
2. The carbon adsorber must reduce the perchloroethylene concentration in the drum to three hundred (300) ppm or less;
3. The dry cleaning control system must be designed so that the gas-vapor stream passes through the secondary carbon adsorber after the final cool-down cycle and immediately before the machine door is opened;
4. The carbon adsorber system must use non-contact steam or hot air for desorption, and must be desorbed in accordance with the manufacturer’s instructions or weekly, whichever is more frequent; and
5. The owner or operator shall measure the perchloroethylene concentration in the drum weekly according to the following specifications:
a. Measurements shall be made using a colorimetric detector tube designed to measure a concentration of three hundred (300) ppmv of perchloroethylene to an accuracy of ± seventy-five (75) ppmv;
b. Colorometric detector tubes shall be used according to the manufacturer’s instructions; and
c. Measurements shall be taken immediately upon opening the door of the dry cleaning machine at the end of the drying cycle in the space above the articles.
23.11 Requirements for Vapor Barriers and General Exhaust Ventilation
A. Any co-located perchloroethylene dry cleaning facility which begins operation after December 2, 2003, shall be equipped with the following before beginning operation:
1. A vapor barrier that encloses the dry cleaning machine(s) or the room where the dry cleaning machine is located. The vapor barrier shall adhere to the following specifications:
a. The vapor barrier shall be constructed of twenty-two (22) mil thick PVC, sheet metal, glass, metal foil face composite board, STRUCTOGlas Class C/III Wall and Ceiling Panels (minimum thickness 0.085 inch) or other materials that are impermeable to perchloroethylene vapor;
b. The vapor barrier shall be constructed in a manner consistent with applicable fire codes, as determined by fire code enforcement agencies;
c. The vapor barrier shall be constructed and maintained such that all joints, seams and openings, except for make-up air and exhaust openings and entry doors, are sealed.
d. Cement floors in the vapor barrier must be coated with an epoxy Novolac coating or other coating that is impermeable to perchloroethylene vapors;
e. The vapor barrier shall be maintained such that it continues to be impermeable to perchloroethylene vapors at all times; and
f. Entry doors shall be kept closed except when a person is entering or exiting the room enclosure.
2. A general exhaust system that is completely separate from the ventilation system(s) serving other areas of the building. The intake of the general exhaust ventilation system must be located near the dry cleaning machinery or connected to the exhaust from the room enclosure and the system must exhaust emissions to the outdoor air. The exhaust system must be operated at all times that the dry cleaning machine(s) is in operation and during maintenance operations and must produce at least one air change per five (5) minutes.
B. A co-located perchloroethylene dry cleaning facility that began operation before December 2, 2003 shall, by the dates specified in § 23.11(C) of this Part, operate a general exhaust system according to the specifications in § 23.11(A)(2) of this Part and either:
1. Do not operate a perchloroethylene dry cleaning machine that is not a closed-loop dry-to-dry machine equipped with a refrigerated condenser, a secondary carbon adsorber and a drying sensor, or
2. Install a vapor barrier that meets the specifications in § 23.11(A)(1) of this Part.
C. Compliance with § 23.11(B) of this Part, is required according to the following schedule:
1. A perchloroethylene dry cleaning facility that is co-located with a residence, a school, a day care center or a business that sells food or food products shall be in compliance with § 23.11(B) of this Part by December 2, 2004, or on and after the date twelve (12) months after the facility is first co-located with a residence, school, day care center or business that sells food or food products, whichever is later. In no case shall the compliance date be later than December 2, 2007.
2. All other co-located perchloroethylene dry cleaning facilities shall be in compliance with § 23.11(B) of this Part on and after December 2, 2007.
23.12 Stack Requirements
A. Perchloroethylene-containing air exhausted from dry cleaning systems must be vented through a vertical stack which extends at least six (6) feet above the building’s roof line.
B. The exhaust stack must not be equipped with a cap, elbow or other device that would interfere with the vertical discharge of the exhaust.
C. The Director may require that a stack be extended higher than six (6) feet or that the location of a stack on a roof be changed if they determine that the location of the stack discharge may cause excessive perchloroethylene exposure to neighbors, neighboring facilities or to other occupants of the building in which the dry cleaning facility is located.
D. Facilities located in buildings that are higher than two (2) stories may apply to the Director for an exemption to § 23.12(A) of this Part.
23.13 Emergency Release Prevention and Response Requirements
A. All dry cleaning machines shall be equipped with a spill containment system capable of containing one hundred twenty-five percent (125%) of the capacity of the largest perchloroethylene-containing tank or vessel in the facility.
B. The owner or operator of dry cleaning equipment shall ensure that:
1. Floor drains and flooring in the vicinity of the dry cleaning equipment are sealed so as to be impermeable to perchloroethylene spills; or
2. Dikes, berms or other containment devices sufficient to prevent spilled perchloroethylene from reaching floor drains and permeable flooring have been placed in areas where spills are most likely to occur and procedures for preventing spill migration have been established and are followed.
C. In the event of a perchloroethylene spill, the owner or operator of the facility must take all reasonable measures to ensure that liquid perchloroethylene is not released to the environment. These measures shall include, where applicable, but are not limited to:
1. Ceasing operation of dry cleaning machines;
2. Increasing room exhaust ventilation;
3. Collecting and containing spilled liquid perchloroethylene;
4. Removing and maintaining containers of collected perchloroethylene in a safe manner; and
5. Notifying co-located businesses and/or residences that a spill has occurred.
D. The facility owner or operator must notify the Department and appropriate state, county or municipal emergency response agencies immediately in the event of a fire, explosion, or a spill that results in the release of liquid perchloroethylene to the environment.
E. The following information must be recorded for each explosion, fire, or perchloroethylene spill:
1. The date, time, duration and nature of the incident;
2. Whether the incident resulted in a release of liquid perchloroethylene to the environment;
3. Agencies notified, and the dates and times of the notification; and
4. Corrective actions taken.
23.14 General Requirements for Perchloroethylene Dry Cleaning Facilities
A. Dry cleaning systems shall be operated and maintained according to the manufacturer’s specifications and recommendations.
B. Washer/extractor and reclaimer doors on transfer machine systems and the doors on dry-to-dry machines shall be kept closed except when necessary for maintenance of the equipment or when articles are being loaded or unloaded;
C. Filtration cartridges must be drained in the filter housing for at least twenty-four (24) hours or vented to the control device before disposal.
D. All perchloroethylene and perchloroethylene-containing waste must be stored in sealed containers with no perceptible leaks.
E. The owner or operator of a dry cleaning facility shall inspect the facility for perceptible leaks at least once per week while the dry cleaning system is operating. Liquid leaks shall be detected by visual inspection for pools or droplets of liquid. Vapor leaks shall be detected using a portable halogenated hydrocarbon detector. The following components must be included in the weekly inspection if present at the facility:
1. Hose and pipe connections, unions, couplings and valves;
2. Machine door gaskets and seatings;
3. Filter head gaskets and seatings;
4. Pumps;
5. Solvent tanks and storage containers;
6. Water separators;
7. Muck cookers;
8. Distillation units;
9. Cartridge filter housings;
10. Diverter valves; and
11. Exhaust dampers.
F. All leaks of perchloroethylene liquid or vapor must be repaired immediately upon detection if no new parts are needed or if replacement parts are available at the facility. If parts are needed and are not available at the facility, a purchase order for those parts shall be issued within two (2) working days. Repair parts shall be installed within five (5) working days of receipt.
G. If parameter values monitored pursuant to the requirements in §§ 23.8(A)(7), 23.9(B), or 23.10(A)(5) of this Part exceed the allowable levels specified in §§ 23.8(A)(1), 23.9(A)(4), or 23.10(A)(2) of this Part, respectively, adjustments or repairs shall be made to the dry cleaning system to meet those limits. All repairs must be done immediately if no parts are needed or if replacement parts are available at the facility. If parts are needed and are not available at the facility, a purchase order for those parts shall be issued within two (2) working days. Repair parts shall be installed within five (5) working days of receipt.
H. Any liquid perchloroethylene that is drained from water separators on reclaimers, dry-to-dry units or carbon adsorbers must be collected using one of the following methods:
1. The liquid shall be drained through a collection tube into containers which have a single small hole for the collection tube and which do not have other gaps or holes; or
2. The liquid shall be drained directly to a storage tank.
I. Fugitive perchloroethylene emissions from any part of a dry cleaning system must not exceed fifty (50) ppm, as measured with a colorimetric detector tube, at any time, except during short-term maintenance operations involving the opening of dry cleaning system components for inspection or repair.
23.15 Reporting and Record Keeping
A. The owner or operator of a perchloroethylene dry cleaning facility shall retain onsite a copy of the design specifications and the operating manuals for each dry cleaning system located at the facility.
B. The owner or operator of a perchloroethylene dry cleaning facility shall maintain the following records in a readily accessible location for at least five (5) years and shall make these records available to the Department upon verbal or written request:
1. A log of perchloroethylene purchases, the date of those purchases, and the receipts for those purchases;
2. The number of loads dry cleaned each calendar month;
3. The dates of weekly inspections conducted pursuant to the requirements in § 23.14(E) of this Part, the locations where perceptible leaks were detected during each inspection, copies of purchase orders issued for parts to repair the leaks, and the dates that the leaks were repaired;
4. The dates when desorption of a carbon adsorber occurred;
5. A record of control equipment maintenance, including the replacement of carbon in a carbon adsorbers;
6. The temperatures recorded pursuant to the requirements in § 23.8(A)(7) of this Part, the dates that those temperatures were recorded and, if a temperature exceeded forty-five degrees Fahrenheit (45°F), copies of the purchase orders issued for repair parts, if applicable, and the date that the dry cleaning equipment or dry cleaning control equipment was repaired;
7. The colorimetric tube concentrations measured pursuant to the requirements in § 23.9(B) of this Part, the dates that those concentrations were measured and, if a concentration exceeded twenty (20) ppmv, copies of the purchase orders issued for repair parts, if applicable, and the date that the dry cleaning equipment or dry cleaning control equipment was repaired;
8. The colorimetric tube concentrations measured pursuant to the requirements in § 23.10(A)(5) of this Part, the dates that those concentrations were measured and, if a concentration exceeded three hundred (300) ppmv, copies of purchase orders issued for repair parts, if applicable, and the date that the dry cleaning equipment or dry cleaning control equipment was repaired; and
9. The records of fires, explosions and spills specified in § 23.13(E) of this Part.
C. On or before April 15 of each year, the owner or operator of a perchloroethylene dry cleaning facility shall report the following information to the Department:
1. Facility name and address;
2. Name and telephone number of the owner or operator of the facility;
3. Name and telephone number of the technical contact for the facility;
4. The amount of perchloroethylene purchased by the facility in the previous calendar year;
5. The amount of perchloroethylene used by the facility in the previous calendar year;
6. The number of loads dry cleaned in each perchloroethylene dry cleaning machine at the facility in the previous calendar year; and
7. A description of any changes to the dry cleaning system made in the previous calendar year.
Title | 250 | Department of Environmental Management |
Chapter | 120 | Air Resources |
Subchapter | 05 | Air Pollution Control |
Part | 23 | Air Pollution Control Regulation No. 23 - Control of Perchloroethylene Emissions from Dry Cleaning Operations |
Type of Filing | Amendment |
Regulation Status | Inactive |
Effective | 12/24/2018 to 01/04/2022 |
Regulation Authority:
R.I. Gen. Laws § 42-17.1-2(19)
R.I. Gen. Laws Chapter 23-23
R.I. Gen. Laws Chapter 42-35
Purpose and Reason:
The purpose of this regulation is to limit perchloroethylene emissions from dry cleaning operations. The Department of Environmental Management, Office of Air Resources is proposing to eliminate portions of the regulation that no longer apply. Additionally, the regulation has been updated to current RI Code of Regulations (RICR) format.
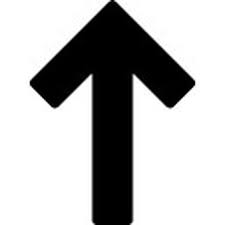
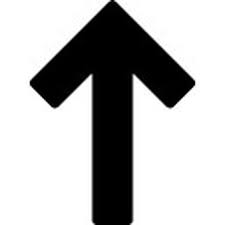
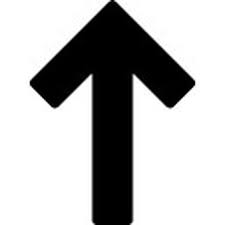
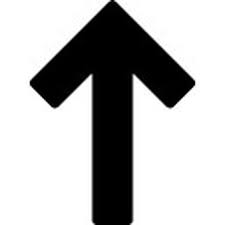
Rulemaking Documents are organized by document type and are part of this rule’s rulemaking record (R.I. Gen. Laws § 42-35-2.3). If multiple documents of the same type are listed below, each is a unique document. If there are multiple Public Notice of Proposed Rulemaking documents, view each document to identify the most recently amended version, as it may be amended at any point during the Public Comment Period.